by Nick Gromicko, CMI®
Laminate flooring is a multi-layer, synthetic flooring product installed as a cost-effective alternative to traditional wood floors. While home inspectors are not required by InterNACHI's Standards of Practice to specifically inspect laminate flooring, knowing something about the various types, manufacture and characteristics can help them spot defects and potential hazards.
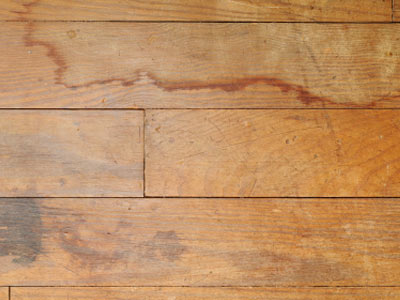
Laminate flooring simulates wood and, less commonly, marble, limestone and granite, using a photograph installed beneath a clear protective layer. This image makes the laminate closely resemble a natural material, but the difference becomes apparent upon close inspection. Homeowners may choose from among common woods, such as maple, oak and pine, as well as exotic species, such as Brazilian cherry, mahogany and walnut. Beneath this layer is an inner core composed of melamine resin and fiberboard materials. Pergo® is the most popular brand of laminate flooring, although it is often mistakenly used to describe all laminate floors. Laminate floor manufacturers include DuPont® and Witex®.
Laminate floors are environmentally friendly -- the paper and wood are made from recycled products -- and easy to maintain, as they are resistant to scratches, dents and demarcations. And, unlike hardwood floors, laminate floors can be installed without any expensive equipment or training. They are more affordable than hardwood floors and they’re often the better choice for homeowners who require an inexpensive floor that is expected to take a beating. Hardwood floors, however, can be sanded and refinished, and tend to add substantial value to the entire house.
Here is a list of defective conditions common to laminate floors:
- gapping. Extreme temperature changes can cause the boards to pull away from one another. Builders should acclimatize laminate flooring to the conditions of the room in which the laminate will be installed;
- peaking. This condition occurs when panels push up against each other at the joints, creating unlevel high points. This defect is common where the boards were not installed with sufficient expansion space. As a remedy, the boards or surrounding molding may be trimmed;
- buckling and warping, which is caused by high humidity, excessive surface moistur
e (such as that leaked from ice makers and pipes), and dampness rising from the sub-floor, along with the lack of a sufficient moisture barrier. Buckling and warping can be limited if a pressure-balancing layer is installed beneath the boards. Hardwood floors, by contrast, are naturally more resistant to moisture damage, as they will swell and shrink to accommodate changes in moisture; - mold, which is caused by excessive moisture. Mold is a potentially serious threat to building materials and the health of sensitive individuals. Refer to InterNACHI’s articles on mold for more information;
- off-registration, in which the patterns on adjacent boards do not match;
- "soft floor." This condition often results when the inner core, made from expanding high-density fiberboard, is subjected to moisture, causing it to swell and fall apart. These boards must be replaced;
- formaldehyde-outgassing, which originates from the melamine resin in various laminate floors. Chemically sensitive individuals may select laminate flooring that has been treated to reduce formaldehyde emissions; and
- sound penetration. Laminate is a “floating floor,” meaning that occupants can hear a tapping echo when someone walks on the floor. Some manufacturers have added acoustical padding to muffle the sound.
Manufacturers’ warranties may cover some of the aforementioned defects, although many restrictions apply. For instance, the floors must be installed to the manufacturer’s specifications, such as leaving vapor barriers and expansion gaps where required. Abuse, accidents, scratches, and many types of water damage are not covered.
Geoff Bostwick of Bostwick Floors in Wapingers Falls, New York, tells InterNACHI, "These guarantees apply only to materials, which cost very little. To replace an individual laminate plank, you need to first remove all of the adjacent planks. This work is time-intensive and is not covered by warranties.”
In summary, laminate floors are inexpensive and strong, but they’re not immune to a variety of defects. An InterNACHI inspector who understands some of these defects and their causes can better advise his clients on appropriate remedies.