by Nick Gromicko, CMI®
Thermal or infrared (IR) imaging in the practice of building inspection has been used to inspect electrical systems for some time now and its use has steadily grown increasingly popular. Since components in electrical systems almost always overheat before they fail, problem areas are more easily and safely found when viewed through an IR camera.
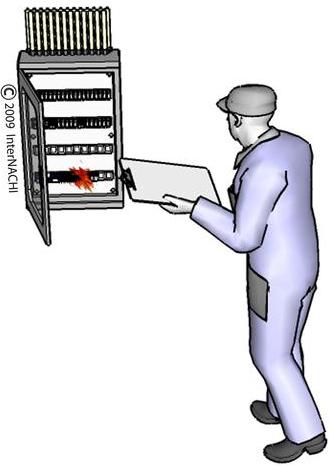
Infrared imaging allows apparent temperatures to be seen as gradient colors, with hotter spots displayed as brighter colors, and cooler (and wetter) spots displayed as darker colors. When a malfunctioning electrical component or connection is generating more heat than it should be, its apparent temperature will make it stand out right away when viewed through thermal imaging.
What kinds of problems can be detected?
During an inspection, electrical equipment, such as distribution panelboards, switch boards, contacts, transformers, receptacles, and service and control panels, can be examined through an IR camera. By viewing apparent temperature differences, inspectors can identify and document problems, such as loose connections and overloaded circuits, which are the most common causes of electrical fires. Other issues, such as transformer cooling problems, induced currents, arcing, and motor-winding faults, also become readily apparent.
Thermal imaging can detect electrical issues that include:
- excessively hot or loose connections;
- overloaded wiring;
- overloaded circuits;
- overloaded transformers;
- overloaded motors;
- arcing; and
- excessive harmonics.
Advantages of Using an IR Camera for Electrical Inspections
Because viewing apparent temperature differences through an IR camera requires no physical contact and can cover a lot of space in one sweep, no other technology allows electrical faults to be found as safely and as quickly as thermal imaging. Another important benefit is that it allows problem areas and components to be located before damage from any serious failure or electrical fire occurs. This helps ensure safety. It can also save money that might otherwise need to spent on extensive repairs.
Here’s a list of advantages of using an IR camera for electrical inspections: 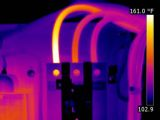
- It’s non-contact, which helps ensure a safe inspection.
- It’s fast and accurate.
- It helps identify problems before they cause serious failure or an electrical fire.
- It’s non-intrusive, so there is no interruption of power during the inspection.
- It can be used as part of inspections that are conducted as preventative maintenance.
- IR equipment is light and portable.
- It provides documentation of problems.
Inspection Tips
When inspecting electrical systems with infrared thermography, it is necessary to use an IR camera. Tools such as spot radiometers and thermal line scanners alone are insufficient for providing documentation and qualitative assessments of electrical systems.
Before beginning the inspection, it is useful to ensure that access is available to all areas and components that will be inspected. The electrical systems can then be examined while operating under a normal load. Any open panels or enclosures are typically inspected first. A panel that shows signs of moisture, is heavily rusted, is buzzing or arcing, or that generally shows any signs of being unsafe should be reported but not opened or touched. Infrared images can be taken from a safe distance for documentation.
Panels and other areas to be inspected that are deemed safe through vis
ual inspection first, such as receptacles, can be examined by line of sight with the infrared camera. It is quick and easy to view all components in most service panels with thermal imaging, and problem areas will be visible as apparent temperature differences. These areas can then be documented by including an infrared image alongside a standard digital photo in the inspection report. One practice that may be helpful is to document similar components operating under similar loads. The side-by-side comparison of a properly functioning component and a similar one that is not operating correctly is a good way to gather additional details to present clear documentation without exceeding InterNACHI's Standards of Practice for conducting a safe electrical inspection.
The thermal images taken are most useful when they are clear and in focus, allowing the most detail to be captured. The same principles apply to standard, visible-light images taken at the same time for comparison. These complementary images should be captured from the same angle and vantage point as the infrared images so that heat signatures detected by thermal imaging can be identified easily with the corresponding components in the visible-light or digital photo.
Infrared cameras that also incorporate the ability to switch over to standard digital photography are especially useful for electrical inspections because they allow for comparison without having to move or change position between photos.
When providing documentation after the inspection, it is useful to include the following:
- the exact locations of any problems found;
- a description of the issue that also includes any nameplate data, and phase or circuit numbers;
- copies of thermal images and corresponding visible-light or digital images;
- the field of view (F-stop) of the infrared lens;
- the manufacturer and model of the camera used; and
- any information regarding conditions that may affect the results, their repeatability, or the interpretation of the problem found.
Using infrared cameras for electrical inspections is safe and quick, and is a great way to document problems that convey useful and easy-to-understand details for property owners. Inspectors will benefit from utilizing this technology in the field.
Consumers should always seek inspectors who are Infrared Certified by looking for the Infrared Certified logo below.